General gasket PHE
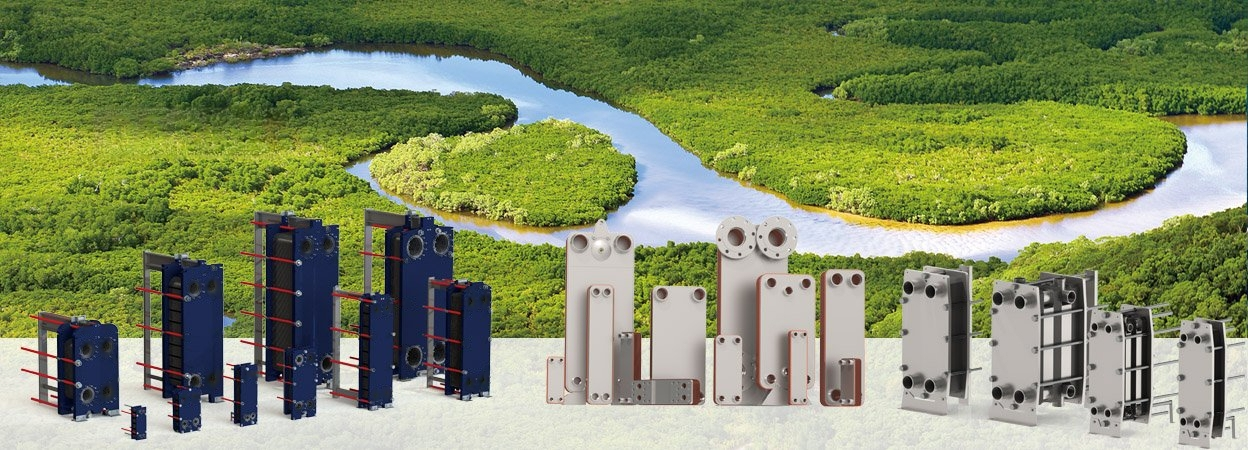
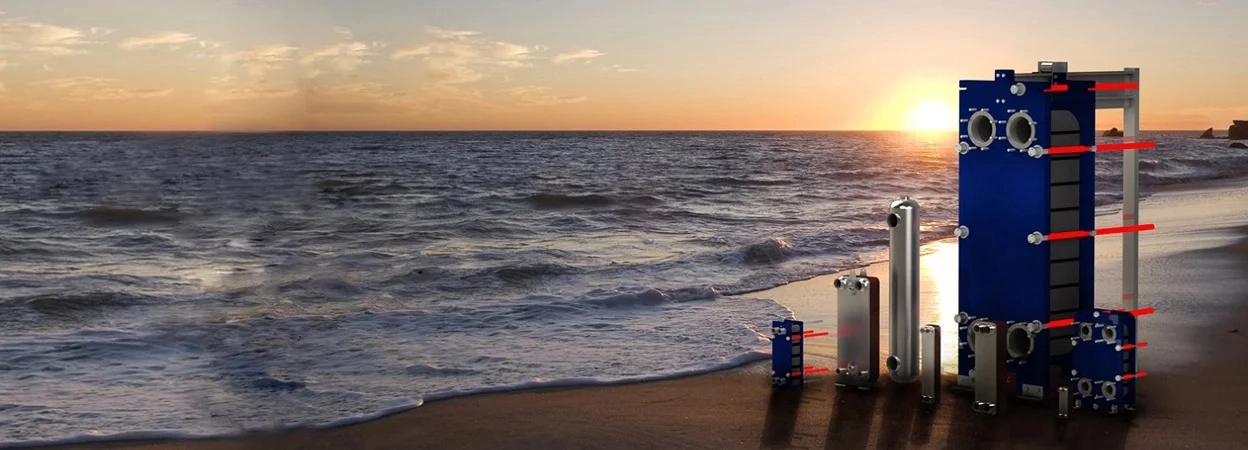
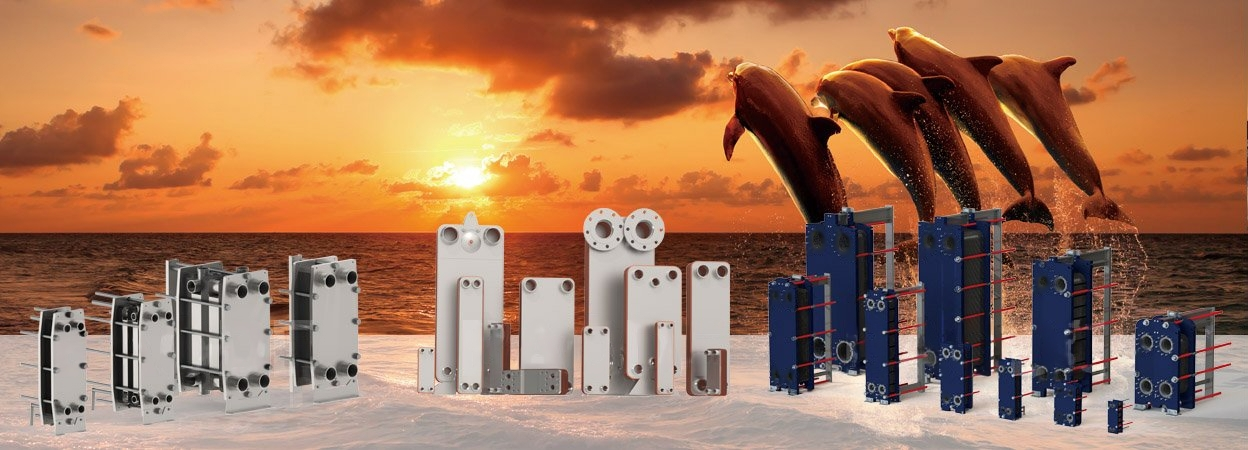
Gasket Plate and Frame heat exchanger


Introduction
A gasketed plate heat exchanger is a type of heat exchanger that consists of a series of corrugated metal plates sealed together with gaskets. The plates are typically made of stainless steel or other materials with good heat transfer properties. The gaskets, usually made of elastomer or other compatible materials, create a seal between the plates and ensure that the fluids remain separate.
Benefits
• High energy efficiency – low operating cost
• Flexible configuration – heat transfer area can be modified
• Easy to install – compact design
• High serviceability – easy to open for inspection and cleaning and easy to clean by CIP
Features
• Gaskets and Sealing:
• Counter-Current Flow:
• Flexibility and Modularity:
• Easy Maintenance and Cleaning:
Applications
• Biotech and Pharmaceutical
• Chemicals
• Energy and Utilities
• Food and Beverages
• Home and Personal care
• HVAC and Refrigeration
• Machinery and Manufacturing
• Marine and Transportation
• Mining, Minerals and Pigments
• Pulp and Paper
• Semiconductor and Electronics
• Steel
• Water and Waste treatment
Connections Available

Model Code Explaination:

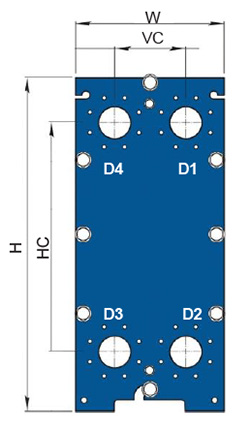
Material | |
Plates | 304, 316L, SMO, C276, NI, Titanium |
Gaskets | NBR, EPDM, FKM |
Flange connections | Carbon steel, Stainless, Titanium, Rubber lined |
Frame plate | Carbon steel, epoxy painted |
Flow direction: | |
Hot In: D1 -> Hot out: D2 , Cold In: D3 -> Cold Out: D4 | |
Hot In: D4 -> Hot out: D3, Cold In: D2 -> Cold Out: D1 |
Model | W | H | HC | VC | Free channel | Connection Standard |
B30B | 180 | 480 | 60 | 357 | 2.5 | DN25 |
B60B | 320 | 920 | 140 | 640 | 2 | DN50 |
B60H | 320 | 920 | 140 | 640 | 3 | DN50 |
B100B | 454 | 1045 | 225 | 719 | 2.55 | DN100 |
B100H | 454 | 1045 | 225 | 719 | 3.95 | DN100 |
B150B | 610 | 1815 | 298 | 1294 | 2.5 | DN150 |
B150H | 610 | 1815 | 298 | 1294 | 3.95 | DN150 |
B200B | 780 | 2260 | 353 | 1478 | 2 | DN200 |
B200P | 780 | 2260 | 353 | 1478 |
| DN200 |
B200H | 780 | 2260 | 353 | 1478 | 4 | DN200 |
B250B | 920 | 2903 | 439 | 1939 | 2.5 | DN250 |
B250H | 920 | 2903 | 439 | 1939 | 4 | DN250 |
B300B | 1150 | 2882 | 596 | 1842 | 3.2 | DN300 / 350 |
LB60B | 320 | 1264 | 140 | 1036 | 2 | DN50 |
LB100B | 480 | 1888 | 225 | 1338 | 2 | DN100 |
LB100P | 480 | 1888 | 225 | 1338 | 3 | DN100 |
LB150B | 610 | 2752 | 288 | 2035 | 2.5 | DN150 |
LB350B | 1154 | 3210 | 578 | 2177 | 2.5 | DN300 / 350 |
SB60H | 400 | 704 | 203 | 380 | 4 | DN50 |
SB200H | 800 | 1405 | 363 | 698 | 4 | DN200 |
Design and Materials
The plates used in a gasketed PHE are generally made from materials like stainless steel (304 or 316L), titanium, SMO, C276, or nickel, depending on the specific application and the type of fluids being handled. The gaskets, on the other hand, are made from materials like NBR (Nitrile Butadiene Rubber), EPDM (Ethylene Propylene Diene Monomer), or FKM (Fluorocarbon rubber), which provide chemical resistance and durability in various environments.
Additionally, the flange connections used in these exchangers can be made from carbon steel, stainless steel, titanium, or rubber-lined materials to ensure strength and compatibility with the fluids being processed.
The frame plate, which holds everything together, is typically made of carbon steel and coated with an epoxy paint to protect against corrosion and wear. This ensures the durability and longevity of the heat exchanger, especially in harsh operating environments.
Working Principle
In a gasketed plate heat exchanger, the hot fluid enters through one side of the exchanger, while the cold fluid enters from the opposite side. As the fluids flow across the corrugated plates, the thermal energy is transferred from the hotter fluid to the colder fluid, without the two fluids ever mixing. This counter-current flow ensures a more efficient transfer of heat, allowing the heat exchanger to operate with high efficiency and reduced energy loss.
The gasket creates the seal between the plates, ensuring that the fluids remain in their respective channels. The gaskets are critical in maintaining the exchanger’s integrity by preventing leaks and ensuring that the fluids don’t cross-contaminate.
Benefits of Gasketed Plate Heat Exchangers
Gasketed plate heat exchangers come with several key benefits, making them ideal for various industries:
High Energy Efficiency
Gasketed PHEs are highly efficient in transferring heat between fluids, ensuring maximum thermal performance with low operating costs. The thin plates and large surface area facilitate effective heat exchange, which means that less energy is required to achieve the desired temperature changes.Flexible Configuration
These exchangers offer great flexibility. The number of plates can be easily adjusted, allowing the heat transfer area to be modified according to specific application needs. This modularity makes gasketed PHEs ideal for systems where capacity needs might change over time.Compact Design
Gasketed PHEs are known for their compact footprint, making them easy to install in tight spaces without sacrificing performance. This compact design is especially useful in industries where space is a premium, such as marine, HVAC, and manufacturing environments.High Serviceability
One of the standout benefits of a gasketed plate heat exchanger is its ease of maintenance. The unit can be easily opened for inspection, cleaning, and gasket replacement without requiring the dismantling of the entire system. Cleaning the plates can often be done via cleaning-in-place (CIP) methods, saving both time and labor costs.
Key Features
Gaskets and Sealing: The elastomer gaskets create an airtight seal between the plates, preventing any leakage of fluids during operation. This ensures safe and efficient heat transfer.
Counter-Current Flow: The counter-current arrangement of fluids maximizes the temperature differential between the two fluids, improving the overall heat transfer efficiency of the system.
Flexibility and Modularity: These heat exchangers can be easily adjusted to match specific operational requirements, offering flexibility in terms of heat transfer area.
Easy Maintenance and Cleaning: The gasketed design allows easy disassembly for cleaning, making it a cost-effective choice for industries requiring frequent maintenance.
Applications of Gasketed Plate Heat Exchangers
Gasketed plate heat exchangers are widely used across various industries due to their versatility and high efficiency. Some of the primary applications include:
- Biotech and Pharmaceutical: For temperature control in fermentation processes and sterilization systems.
- Chemical Processing: For cooling, heating, and condensing applications in reactors and separators.
- Energy and Utilities: Used in district heating, power plants, and other energy-related processes.
- Food and Beverage Industry: For pasteurization, cooling, and heating of liquid foods, as well as in brewing and dairy processes.
- HVAC and Refrigeration: These heat exchangers are commonly used in chillers, condensers, and evaporators for maintaining climate control in buildings.
- Water and Waste Treatment: For treating wastewater and ensuring efficient heat recovery in water purification systems.
Customization Options
Gasketed plate heat exchangers can be tailored to meet specific needs by choosing different materials for the plates, gaskets, and frame components. Depending on the operational requirements, configurations for flow directions and connection standards are available to optimize performance.
For example, the B-series models of gasketed plate heat exchangers vary in terms of size, flow capacity, and connection types, making it easy to select the perfect model for your application. Some models like the B60H and B200H offer higher flow rates, while others, such as the B100B or B150B, are more compact and designed for medium-capacity applications.
Conclusion
In conclusion, gasketed plate heat exchangers offer a versatile, efficient, and customizable solution for industries requiring efficient heat transfer. Their compact design, ease of maintenance, and flexibility make them an excellent choice for a wide range of applications. Whether you’re working in energy, food processing, HVAC, or water treatment, a gasketed PHE can help optimize your system’s performance, reduce energy consumption, and ensure reliable operation.
At Mge Tech, we pride ourselves on offering top-tier gasketed plate heat exchangers that are tailored to meet the needs of our clients across the globe. With a commitment to quality, innovation, and customer satisfaction, we aim to provide the best possible solutions for all your heat transfer needs.