Evaporator GPHE
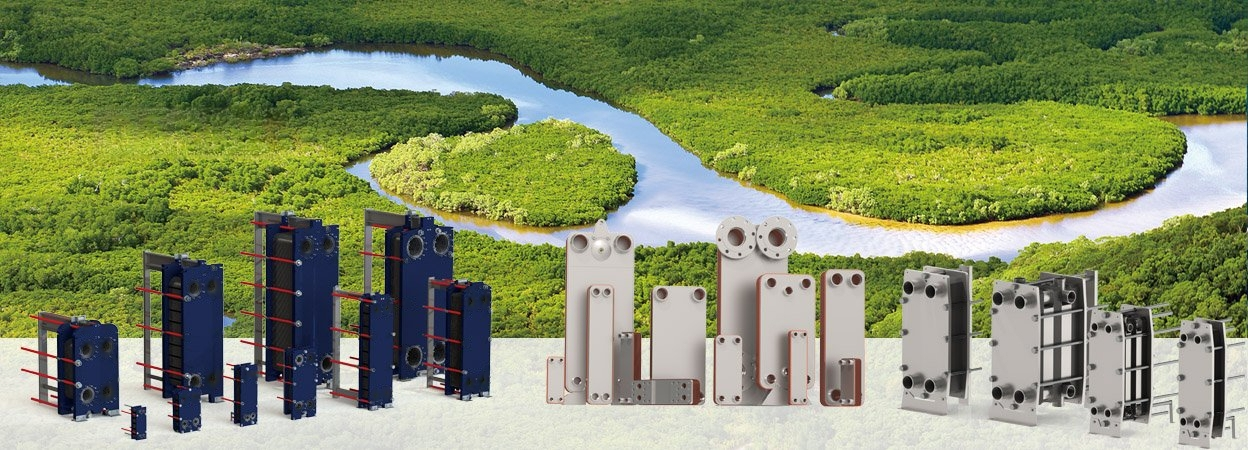
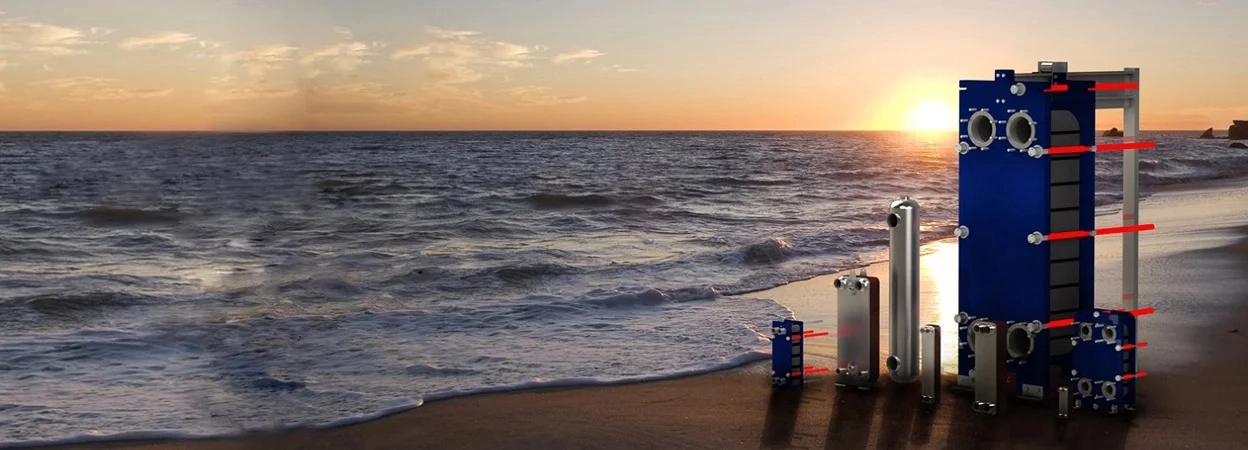
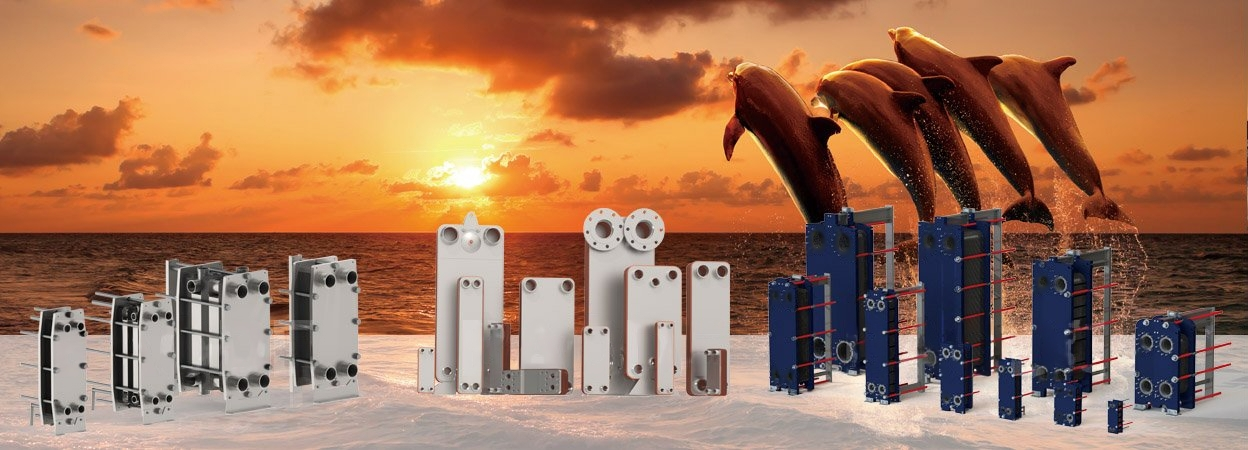
Vapor Gasket heat exchanger
How it works
Vapor GPHE is purpose-built for evaporation, featuring two compact inlet feed connections and a spacious outlet dedicated to vapor and concentrate. It is equipped with one sizable inlet and two smaller outlets for condensate. The design of Vapor GPHE incorporates plates welded in pairs, allowing for effective condensation of heating steam in the welded channel, while the evaporated product smoothly flows through the gasketed channels.
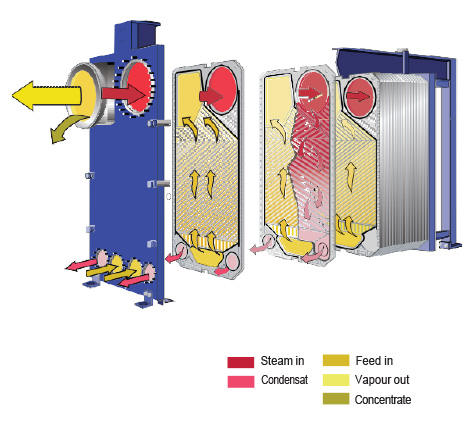
Benefits
Enhanced thermal conductivity
The arrangement of corrugated plates induces intense turbulence, resulting in significantly higher heat transfer efficiency compared to traditional
shell-and-tube evaporators. Vapor GPHE excels particularly in scenarios with high concentration and viscosity, effortlessly handling temperature variations as low as 3–4°C. This quality proves exception- ally advantageous when integrated into TVR and MVR systems.
Minimal fouling and effortless maintenance
The extensive plate turbulence enables highly effective chemical cleaning procedures. Due to the reduced volume capacity, only minute quantities of cleaning agents are necessary in comparison to shell-and-tube systems. Furthermore, the flexible design of Vapor GPHE ensures easy accessibility to heat transfer surfaces for inspection or mechanical cleaning.
Flexible capacity expansion
One prominent advantage of Vapor GPHE is its capability to increase or decrease capacity by adding or removing cassettes within the existing framework. This feature stands in stark contrast to shell-and-tube evaporators, where capacity remains fixed upon installation.
Saving
The remarkable heat transfer efficiency translates into a substantial reduction in required heat transfer surface area compared to shell-and-tube evaporators. Consequently, Vaper GPHE becomes highly cost-effective, especially when dealing with demanding materials like SMO, titanium, nickel, and Hastelloy.
Additionally, the compact and adaptable design of Vapor GPHE greatly diminish- es expenses related to transportation, assembly, and installation when compared to shell-and-tube units.
Enhanced product quality
The exceedingly low hold-up volume within Vapor GPHE means that only a negligible amount of product remains inside the evaporator at any given time. This brief exposure time to the evapora- tor proves highly beneficial for heat-sen- sitive products, ensuring improved product quality.
Applications
• Biotech and Pharmaceutical
• Chemicals
• Energy and Utilities
• Food and Beverages
• Water and Waste treatment
Dimensional drawing
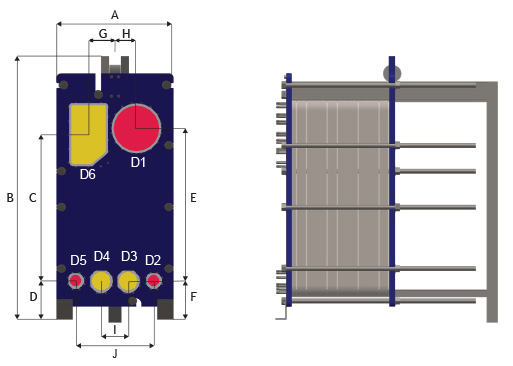
Technical data
Plate Type | Free channel, mm |
Semi-welded | 6 / 6.5 |
Materials | 10 |
Heat transfer plates | 316/316L, 904L, 254 |
Field gaskets | NBR, EPDM |
Ring gaskets | NBR, EPDM, FKM |
Flange connections | Metal lined: stainless steel, nickel, titanium |
Frame & pressure plate | Carbon steel with painted |
Model | A | B | C | D | E | F | G | H | I | J | D1 | D2/D5 | D3/D4 | D6 |
EC350 | 1160 | 2610 | 1430 | 385 | 1576 | 394 | 271 | 252 | 290 | 806 | 350 | DN100 | DN150 | DN350 |
EC500 | 1160 | 2610 | 1509 | 394 | 1532 | 438 | 278 | 223 | 290 | 806 | 400 | DN100 | DN150 | DN500 |
EC650 | 1380 | 3210 | 2028 | 430 | 2158 | 414 | 294 | 329 | 300 | 913 | 450 | DN150 | DN150 | DN650 |
Operational data
Max. design pressure | Max. design temperature (°C/°F) |
6.0/ 8.0 barg | 180/356 |
Extended pressure and temperature rating may be available
Evaporation processes are crucial across several industries, including biotechnology, pharmaceuticals, food processing, chemicals, and water treatment. To meet the demanding needs of these industries, Vapor Gasket Plate Heat Exchangers (GPHEs) offer an innovative alternative to traditional shell-and-tube evaporators. Vapor GPHEs are designed to enhance thermal efficiency, minimize fouling, and offer unparalleled flexibility in operation. This article provides an in-depth look into how Vapor GPHEs work, their key benefits, applications, and technical specifications.
How Vapor GPHE Works
The Vapor GPHE is purpose-built to optimize evaporation processes. It features a smart design with two compact inlet connections for the feed product and a spacious outlet for the vapor and concentrated product. It also includes one large inlet and two smaller outlets for handling the condensate.
Each unit consists of plates welded in pairs, which form the core heat transfer surfaces. The welded channels are designed for effective condensation of the heating steam, while the evaporated product flows smoothly through the gasketed channels. This specialized configuration ensures the separation of the fluids and maximizes heat transfer efficiency.
Benefits of Vapor Gasket Plate Heat Exchangers
Enhanced Thermal Conductivity and Heat Transfer Efficiency
The corrugated plates inside the GPHE create intense turbulence within the fluid streams, leading to superior heat transfer efficiency compared to shell-and-tube evaporators. This high turbulence ensures rapid evaporation, even for fluids with high concentrations or viscosities. The GPHE also performs well under low-temperature differentials, with the ability to operate efficiently with temperature differences as low as 3–4°C. This makes it an ideal solution for use in Thermal Vapor Recompression (TVR) and Mechanical Vapor Recompression (MVR) systems.Minimal Fouling and Easy Maintenance
One of the key advantages of Vapor GPHEs is the extensive turbulence that reduces fouling on the heat transfer surfaces. The exchanger’s design enables effective chemical cleaning with minimal use of cleaning agents, which lowers operating costs compared to traditional systems. Moreover, the exchanger’s flexible design allows easy access to plates for inspection and mechanical cleaning when necessary, ensuring long-term reliability.Flexible Capacity Expansion
Unlike shell-and-tube systems, where capacity is fixed upon installation, Vapor GPHEs provide modular flexibility. Capacity can be increased or reduced by adding or removing cassettes (plate pairs) from the existing framework, making them highly adaptable to changing operational needs.Cost Savings
The superior heat transfer efficiency of Vapor GPHEs means that less heat transfer surface area is required to achieve the same thermal performance as a shell-and-tube evaporator. This reduction in required surface area leads to significant savings, especially when expensive materials such as SMO, titanium, nickel, or Hastelloy are used. Additionally, the compact design of GPHEs reduces transportation, assembly, and installation costs, making them a cost-effective solution for industries with space and budget constraints.Improved Product Quality
Vapor GPHEs are designed with low hold-up volumes, meaning only small amounts of product remain inside the exchanger at any given time. This short exposure to the evaporator minimizes the risk of product degradation, especially for heat-sensitive products. This feature is particularly beneficial in the pharmaceutical and food and beverage industries, where maintaining product integrity is essential.
Applications of Vapor GPHEs
Vapor GPHEs are versatile and can be employed across various industries for efficient evaporation and heat transfer:
- Biotech and Pharmaceutical: Used in evaporation processes for fermentation products, vaccines, and purification systems, ensuring high-quality end products.
- Chemical Processing: Suitable for concentrating chemical solutions and recovering valuable solvents.
- Food and Beverage: Used for applications such as milk concentration, juice processing, and sugar production, where gentle heat treatment preserves the product’s flavor and nutrients.
- Water and Waste Treatment: Helps in concentrating wastewater streams and removing contaminants, supporting efficient water recycling processes.
- Energy and Utilities: Integrated into thermal and mechanical vapor recompression (TVR/MVR) systems to improve energy efficiency.
Materials:
- Heat Transfer Plates: Stainless Steel (316/316L, 904L), Titanium, C-276
- Field Gaskets: NBR (Nitrile), EPDM (Ethylene Propylene Diene Monomer)
- Ring Gaskets: NBR, EPDM, FKM
- Flange Connections: Stainless Steel, Nickel, Titanium
- Frame and Pressure Plate: Carbon Steel with Protective Paint
Operating Conditions:
- Maximum Design Pressure: 6.0 / 8.0 barg
- Maximum Design Temperature: 180°C (356°F)
These technical features ensure that Vapor GPHEs can handle a wide range of industrial conditions with ease, making them reliable and efficient solutions for demanding applications.
Comparison with Shell-and-Tube Evaporators
Vapor GPHEs offer several advantages over conventional shell-and-tube evaporators:
- Higher Efficiency: The corrugated plates in GPHEs induce more turbulence, resulting in better heat transfer.
- Compact Design: GPHEs take up less space and are easier to install and transport.
- Flexible Capacity: GPHEs allow easy capacity adjustments by adding or removing plates, unlike fixed-capacity shell-and-tube units.
- Lower Maintenance Costs: Reduced fouling and easy cleaning minimize downtime and maintenance expenses.
- Material Savings: With less surface area required for the same performance, GPHEs reduce costs when using expensive materials.
Conclusion
Vapor Gasket Plate Heat Exchangers (GPHEs) represent a significant advancement in evaporation technology, offering enhanced efficiency, flexibility, and product quality. Their modular design, low fouling tendency, and cost-saving features make them a superior choice compared to traditional shell-and-tube systems.
Whether it’s in pharmaceuticals, food processing, water treatment, or chemical industries, Vapor GPHEs provide the perfect combination of performance and adaptability. With the ability to handle challenging fluids, accommodate process changes, and maintain product quality, Vapor GPHEs are well-suited for industries aiming to optimize their evaporation processes.
At Mge Tech, we are committed to delivering cutting-edge solutions tailored to meet your operational needs. Our Vapor GPHEs are designed with high-quality materials, ensuring reliability, durability, and efficiency for your business.