Copper Brazed PHE
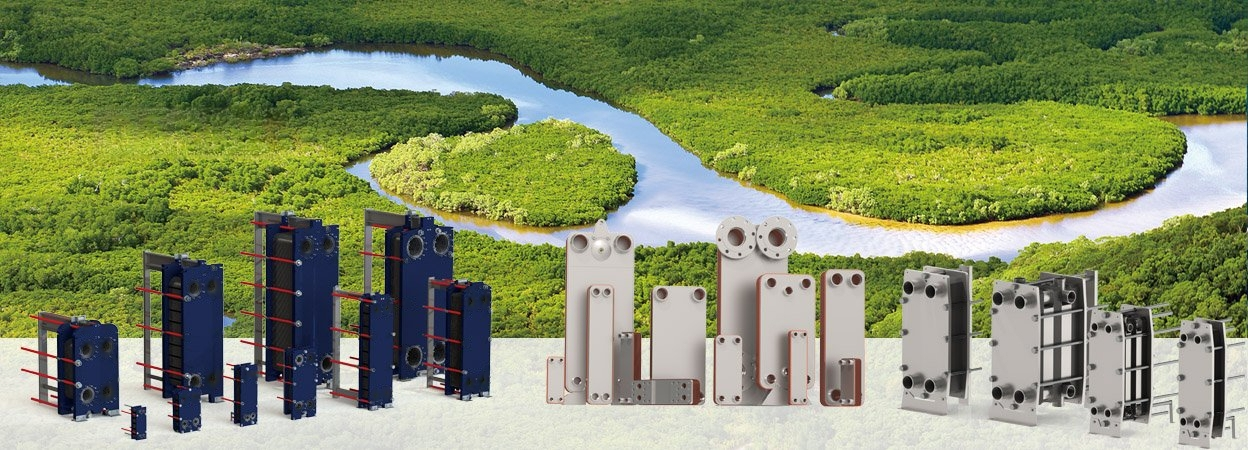
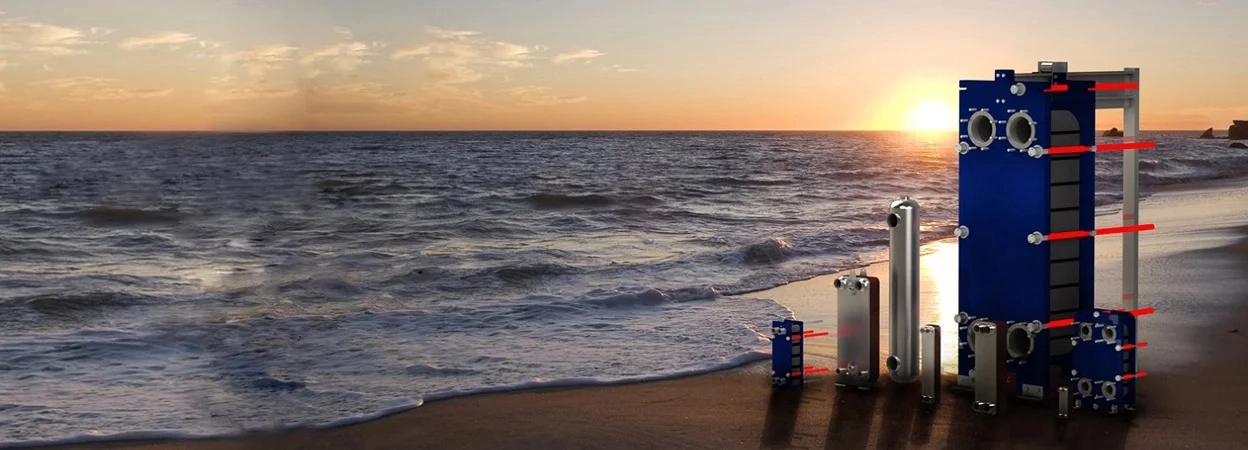
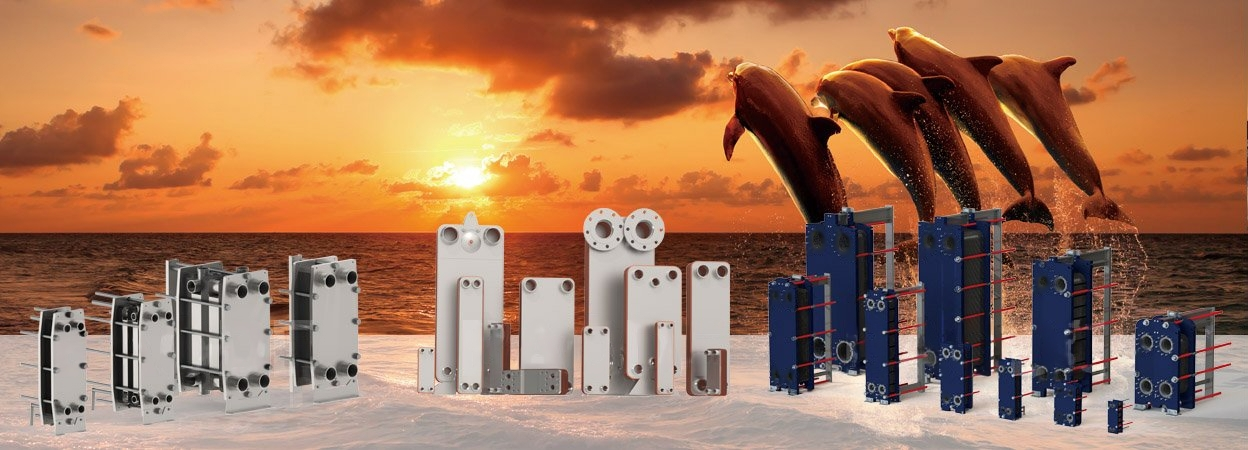
Brazed Plate Heat Exchanger
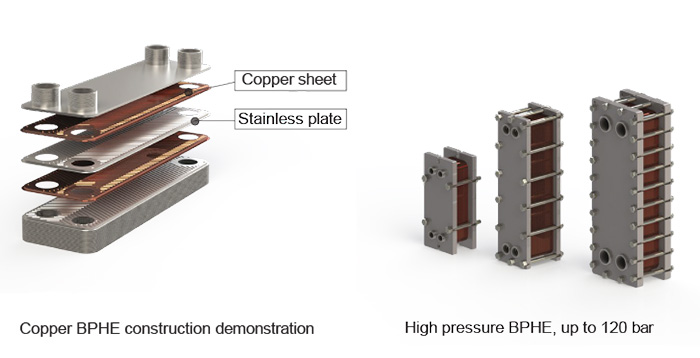
Brazed heat exchanger (BPHE) is a type of compact heat exchanger that consists of corrugated metal plates that are brazed together to form a single unit. The brazing process involves melting a filler material, tipically copper-based alloy (Stainless or Nickle are available) between the plates to create a strong and leak-proof joint.
The main advantages of brazed heat exchangers include their high heat transfer efficiency, compact size, and reliability.
Features :
Compact Size: Brazed heat exchangers corrugated plates create multiple flow channels, maximizing the heat transfer surface area within a small footprint. This makes them ideal for applications where space is limited.
Efficient Heat Transfer: The corrugated plates in a brazed heat exchanger create turbulence in the fluid flow, enhancing heat transfer efficiency. The turbulent flow promotes better mixing of the fluids and minimizes the formation of stagnant zones, leading to improved heat transfer rates.
High Thermal Efficiency: The brazing process used in the construction of these heat exchangers ensures a highly conductive joint between the plates.
Reduced Fouling: The design of brazed heat exchangers with smooth and continuous surfaces minimizes the potential for fouling. The absence of gaskets or crevices reduces the likelihood of accumulation of debris or scale, resulting in lower maintenance requirements and improved overall performance.
Wide Range of Applications:
– HVAC systems
– Refrigeration
– Process cooling
– Industrial heating/ cooling.
– liquid-to-liquid and gas-to-liquid heat transfer processes

- Connection 2. Front pressure plate 3. Channel plates 4. End pressure plate 5. Hot fluid 6. Cold fluid
Flow principle
The basic flow principle in a brazed plate heat exchanger is parallel to achieve the most efficient heat transfer process.In a single pass design, all connections are located on one side of the heat exchanger, making installation very easy.
The flow principle of a brazed heat exchanger is based on the counter-current flow configuration, where the two fluids involved in the heat transfer process flow in opposite directions. e.g the picture A and B
Connections

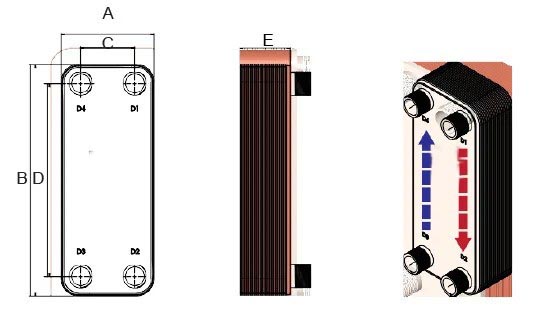
Material | |
Cover plates material | 304 stainless |
Flow plates | 316L/304 stainless |
Connections | 304 stainless |
Brazing material | Copper / Ni / Stainless |
Single circuit BPHE data (unit: mm)
Model | Design Pressure | A | B | C | D | E | Chinnel Volume L |
BL6 | 30/45 | 55 | 119 | 26 | 91 | 7+1.29N | 0.0053 |
BL12 | 30/45 | 76 | 152 | 42 | 120 | 7+1.29N | 0.01 |
BL13 | 30/45 | 76.5 | 194 | 40 | 154 | 8+1.05N | 0.0093 |
BL14 | 30/45 | 76 | 206 | 42 | 172 | 8.6+2.3N | 0.027 |
BL14D | 10 | 71 | 186 | 40 | 154 | 7.5+2.26N | 0.026 |
BL15A | 10 | 83 | 193 | 40 | 154 | 7+2.26N | 0.029 |
BL14W | 30/45 | 78 | 206 | 42 | 172 | 7.5+2.26N | 0.028 |
BL16 | 30/45 | 78 | 206 | 42 | 172 | 7.5+2.26N | 0.028 |
BL17 | 30 | 85 | 202 | 39 | 153 | 24.5+2.31N | 0.031 |
BL18 | 10 | 91 | 210 | 50 | 162 | 9+3.3N | 0.053 |
BL20 | 30/45 | 77 | 317 | 42 | 282 | 8+2.31N | 0.042 |
BL20W | 30/45 | 75 | 315 | 42 | 282 | 11+2.25N | 0.042 |
BL21 | 45 | 76 | 312 | 42 | 278 | 6.6+1.23N | 0.021 |
BL25 | 30/45 | 92 | 322 | 39 | 268 | 8+1.55N | 0.032 |
BL26 | 30/45 | 109 | 310 | 50 | 250 | 10.6+2.35N | 0.057 |
BL26W | 30/45 | 106 | 306 | 50 | 250 | 10.9+2.25N | 0.057 |
BL30 | 30/45 | 124 | 304 | 70 | 250 | 12+2.31N | 0.069 |
BL50 | 30/45 | 108 | 525 | 50 | 466 | 9.5+2.31N | 0.097 |
BL60 | 30/45 | 119 | 526 | 63 | 470 | 9.4+2.31N | 0.11 |
BL95A | 30/45 | 187 | 616 | 92 | 519 | 10.2+2.31N | 0.2 |
BL95B | 30/45 | 187 | 616 | 92 | 519 | 11+2.81N | 0.25 |
BL95C | 30/45 | 187 | 616 | 92 | 519 | 11+2.81N | 0.25 |
BL120 | 30/45 | 245 | 529 | 174 | 456 | 12.4+2.31N | 0.24 |
BL122 | 30/45 | 246 | 529 | 174 | 456 | 12.4+2.31N | 0.24 |
BL125 | 30 | 248 | 530 | 159 | 441 | 12+1.95N | 0.2 |
BL180 | 30/45 | 256 | 846 | 160 | 750 | 8+2.31N | 0.4 |
BL190 | 15/21/30 | 307 | 698 | 179 | 567 | 9+2.81N | 0.49 |
BL195 | 15/21/30 | 306 | 694 | 179 | 567 | 11.2.31N | 0.39 |
BL200 | 15/21/30 | 320 | 740 | 188 | 603 | 12+2.75N | 0.54 |
BL350 | 30 | 304 | 981 | 179 | 854 | 11.5+2.31N | 0.55 |
BL600 | 15/21 | 436 | 140 | 220 | 1190 | 16.3+2.8N | 1.4 |
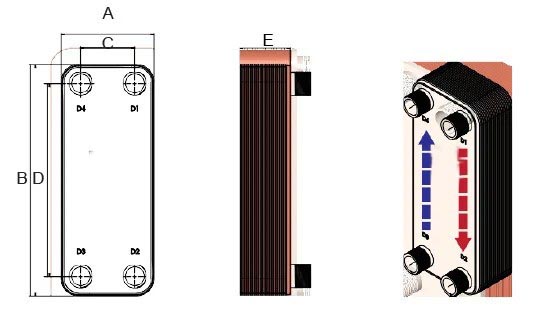
Model | Design Pressure (bar) | A | B | C | D | F | E | Channel Volume L |
BL100 | 30/45 | 248 | 496 | 405 | 157 | 405 | 7+1.29N | 0.2 |
BL100E | 30/45 | 248 | 495 | 411 | 159 | 369 | 10+2.09N | 0.2 |
BL100EW | 30/45 | 243 | 491 | 411 | 159 | 369 | 10+2.03N | 0.2 |
BL130AS | 45 | 293 | 532 | 397 | 177 | 399 | 12.3+2.05N | 0.27/0.24 |
BL210 | 30/45 | 320 | 737 | 568 | 205 | 631 | 8+2.61N | 0.5 |
A dual system BPHE (Brazed Plate Heat Exchanger) refers to a brazed plate heat exchanger that is specifically designed to accommodate two separate and independent fluid circuits within a single compact unit. It consists of two separate sets of plates, each forming a distinct flow path for a different fluid
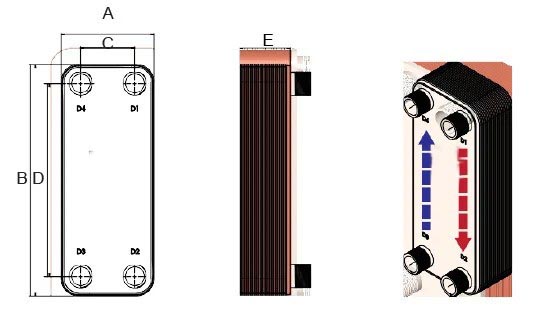
Part-load efficiency also decreases with these arrangements, because the flow arrangement means that only 50% of the secondary fluid undergoes heat exchange. The evaporation temperature at part load may therefore decrease, reducing system efficiency and increasing the risk of freezing. Instead, True Dual technology BPHEs have two independent refrigerant circuits combined with a common secondary fluid circuit. A True Dual heat exchanger is shown in Figure 1.
A True Dual BPHE running with both circuits active operates no differently from a high-efficiency single circuit evaporator with full contact between refrigerant and secondary fluid.

Even if one refrigerant circuit is closed, i.e. half-load operation, all secondary fluid channels remain in contact with the active refrigerant channel (see Figure.2). All the secondary fluid will still receive heat exchange, and the leaving water temperature will therefore be the same as for full-load operation provided the water flow is also halved. This allows the part-load evaporation temperature to remain at a high level, resulting in increased efficiency at part load. Because secondary fluid channels will surround the active refrigerant circuit, the evaporating process will also remain fully stable.
For a schematic system sketch of a True Dual system, see Figure 3.

Asymmetrical brazed plate heat exchanger.
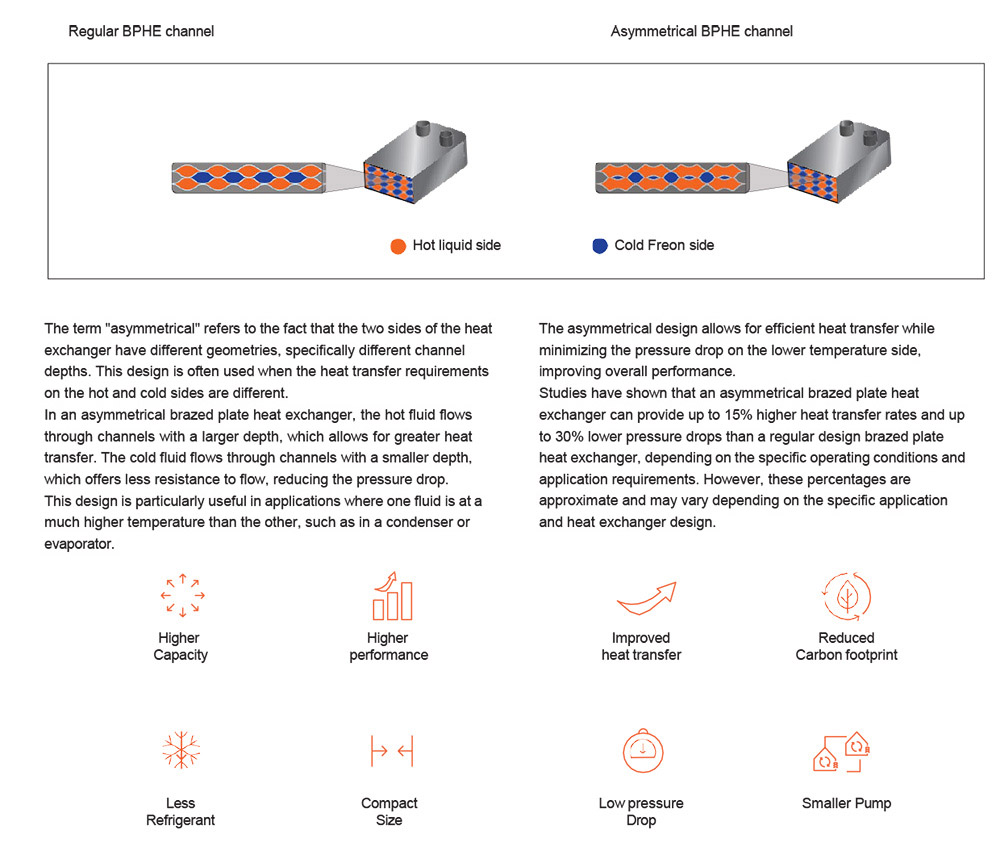
Model | Design Pressure | A | B | C | D | E | Channel Volume L |
BL37AS | 30/45 | 121 | 332 | 68 | 279 | 11.3+1.55N | 0.05/0.04 |
BL40AS | 30/45 | 119 | 376 | 72 | 329 | 12+1.55N | 0.044/0.066 |
BL61AS | 30/45 | 118 | 524 | 63 | 470 | 10.5+1.91N | 0.092/0.075 |
BL95AS | 30 | 185 | 613 | 92 | 519 | 11.3+2.07N | 0.2/0.16 |
BL150AS | 21/30 | 266 | 696 | 122/131 | 564/545 | 10+2.31N | 0.36/0.3 |
Brazed Plate Heat Exchangers (BPHEs) are compact and efficient heat exchangers designed to transfer thermal energy between fluids in a wide range of applications, including HVAC, industrial cooling, refrigeration, and heating systems. These units consist of corrugated metal plates, which are brazed together to form a strong, leak-proof structure. The brazing process involves melting a filler material, typically copper or nickel, between the plates to ensure durability and thermal conductivity.
BPHEs are highly valued for their high heat transfer efficiency, reliability, and compact size, which make them ideal for space-constrained installations. These exchangers perform exceptionally well in liquid-to-liquid and gas-to-liquid applications, providing superior performance in both part-load and full-load conditions.
How Brazed Plate Heat Exchangers Work
The working principle of a BPHE is based on counter-current flow, meaning the hot and cold fluids flow in opposite directions through adjacent channels created by the corrugated plates. This flow configuration ensures maximum heat transfer efficiency by maintaining a consistent temperature gradient throughout the exchanger.
In single-pass designs, all connections are located on one side of the heat exchanger, making installation easier and more convenient. The corrugated plates promote turbulence within the fluid channels, enhancing thermal performance by preventing stagnant zones and ensuring efficient mixing of fluids.
Key Features of Brazed Plate Heat Exchangers
Compact Size
BPHEs offer a high heat transfer surface area within a small footprint, making them perfect for applications where space is limited. Their compact design reduces the need for bulky equipment and lowers installation costs.Efficient Heat Transfer
The turbulent flow created by the corrugated plates improves heat exchange efficiency by promoting thorough mixing of the fluids. This design ensures optimal thermal performance with minimal energy loss.High Thermal Conductivity
The brazing process used to construct BPHEs ensures highly conductive joints between plates, facilitating efficient heat transfer between fluids.Reduced Fouling
BPHEs feature smooth and continuous surfaces that prevent debris and scale from accumulating. The absence of gaskets eliminates crevices where contaminants could build up, ensuring low maintenance and extended service life.
Applications of Brazed Plate Heat Exchangers
BPHEs are used across multiple industries for various thermal management tasks, including:
- HVAC Systems: Heat recovery in air conditioning systems, chilled water loops, and district heating networks.
- Refrigeration: Applied in condensers and evaporators to optimize energy efficiency in refrigeration systems.
- Industrial Cooling: Removes excess heat from manufacturing processes and maintains equipment temperature.
- Process Cooling and Heating: Used in chemical plants, food processing units, and pharmaceutical production for temperature regulation.
- Liquid-to-Liquid and Gas-to-Liquid Heat Transfer: Facilitates heat exchange between different fluid types, including refrigerants and water.
Types of Brazed Plate Heat Exchangers: Single and Dual Circuits
Single-Circuit BPHEs
Single-circuit BPHEs have one flow circuit for each fluid, and all connections are located on one side of the unit. This design simplifies installation and operation, making it ideal for straightforward heat transfer applications such as HVAC or industrial cooling systems.
Dual-Circuit BPHEs
Dual-circuit BPHEs are designed to accommodate two independent fluid circuits within a single compact unit. Each circuit operates independently, allowing for better part-load efficiency and operational flexibility. Even when one refrigerant circuit is inactive, the secondary fluid circuit remains in full contact with the active refrigerant, ensuring stable operation and consistent thermal performance.
True Dual Technology further improves efficiency by ensuring that all secondary fluid channels are surrounded by active refrigerant channels, even during part-load conditions. This design minimizes the risk of freezing and maintains the evaporating process at optimal levels, resulting in superior part-load efficiency.
Asymmetrical Brazed Plate Heat Exchangers
Asymmetrical BPHEs are designed with different flow paths on each side, accommodating varying flow rates or heat loads between two fluids. These exchangers are particularly useful when the primary and secondary fluids have different thermal properties. By optimizing the flow pattern, asymmetrical BPHEs maintain high heat transfer efficiency without increasing pressure drop.
Materials Used in Brazed Plate Heat Exchangers
BPHEs are constructed using durable materials to ensure long-lasting performance and resistance to corrosion:
- Cover Plates: 304 Stainless Steel
- Flow Plates: 316L or 304 Stainless Steel
- Connections: 304 Stainless Steel
- Brazing Material: Copper or Nickel (Stainless options are also available for highly corrosive environments)
These materials allow BPHEs to operate in high-temperature and high-pressure environments, handling aggressive fluids with ease.
These models offer varying capacities and sizes to meet the specific requirements of different industrial applications. The maximum operating pressure ranges from 15 to 45 bar, ensuring durability under extreme conditions.
Advantages of Brazed Plate Heat Exchangers Over Traditional Systems
Higher Efficiency
BPHEs offer better heat transfer efficiency compared to traditional shell-and-tube exchangers, thanks to the counter-current flow and turbulent mixing of fluids.Compact Design
The small footprint of BPHEs allows them to fit into tight spaces and reduces installation costs, making them ideal for applications with space constraints.Low Maintenance Requirements
With no gaskets and smooth internal surfaces, BPHEs require minimal cleaning and are less prone to fouling, ensuring reliable long-term operation.Lower Cost
BPHEs are more cost-effective than other heat exchangers due to their modular design, reduced material usage, and low maintenance needs.
How to Choose the Right BPHE for Your Application
Selecting the appropriate BPHE depends on several factors, including:
- Flow Rates: Ensure the BPHE can handle the maximum expected flow of both fluids.
- Operating Temperatures and Pressures: Choose materials that can withstand your application’s conditions.
- Thermal Load: Calculate the required heat transfer area to meet your process needs efficiently.
- Space Constraints: Consider the physical dimensions of the exchanger to ensure it fits into your available space.
Conclusion
Brazed Plate Heat Exchangers (BPHEs) provide a compact, efficient, and reliable solution for heat transfer in HVAC, refrigeration, industrial cooling, and process heating applications. Their high thermal efficiency, reduced fouling, and low maintenance requirements make them a cost-effective choice for industries looking to optimize energy usage and improve operational efficiency.
The availability of single and dual-circuit designs further enhances their versatility, making them suitable for both part-load and full-load operations. Whether you need an efficient evaporator, condenser, or heat recovery unit, BPHEs deliver exceptional performance and durability.
At Mge Tech, we offer a wide range of BPHE models tailored to meet your specific requirements. Contact us today to learn how our brazed plate heat exchangers can improve your processes and help you achieve your operational goals.